LATEST Blog
Blog Categories:
All Blog:
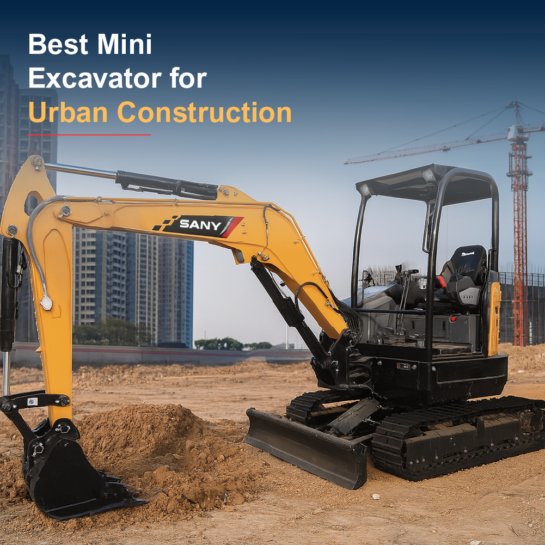
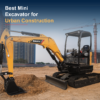
Best Mini Excavator for Urban Construction
Urban construction projects present unique challenges that require specialized equipment. Confined spaces, noise restrictions, and environmental considerations all demand machines that are compact yet powerful. When selecting equipment for urban construction, several key factors must be considered, including size limitations, noise output, emissions, and versatility. The right equipment can make the difference between project success and costly delays in these challenging settings. Sany's line of mini excavators offers the perfect solution for construction professionals working in urban environments. Let's explore the best options from Sany's catalogue and the key factors to consider when selecting the right mini excavator for your urban construction needs. How to Choose the Right Excavator for Urban Construction Construction professionals working in urban environments must carefully select equipment that balances power with maneuverability. Mini excavators, compact loaders, and other space-efficient machinery have become essential tools for city projects, allowing crews to work effectively even in tight quarters. 1. Size and Maneuverability In urban construction, space constraints often determine equipment selection. Sany's mini excavators feature zero tail swing designs that allow operation in tight spaces without sacrificing performance. The SY20U and SY27U are particularly effective for navigating between existing structures, working in alleyways, or operating in partially completed buildings. 2. Noise Levels and Environmental Considerations Urban construction sites frequently face strict noise ordinances. Sany's mini excavators incorporate advanced sound dampening technology and efficient engines that reduce operational noise—a critical factor when working near residential areas or during restricted hours in city centers. 3. Fuel Efficiency and Operating Costs With rising fuel costs and environmental concerns, efficiency is paramount. Sany's mini excavators feature optimized hydraulic systems and fuel-efficient engines that maximize productivity while minimizing fuel consumption. The precision-engineered components ensure less downtime and lower maintenance costs over the equipment's lifecycle. 4. Versatility and Attachments Urban projects often require multiple functions from a single machine. Sany's excavators are equipped with various attachments that transform these machines into versatile tools capable of handling diverse tasks—from breaking concrete to precision grading—without requiring additional equipment in crowded urban sites. Right Excavator for Urban Projects Urban environments demand construction equipment that can navigate tight spaces without sacrificing performance. Sany's mini excavator lineup is specifically designed to meet these challenges, offering compact machines that deliver exceptional power and precision. SY20U: Unmatched Accessibility for Extremely Limited Spaces Weighing just 1.98 tons, the SY20U is Sany's most compact offering, making it ideal for projects in extremely…
read more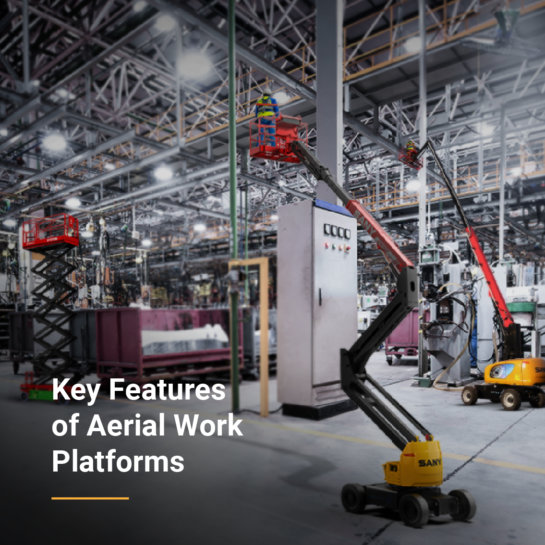
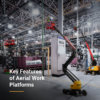
Key Features of Aerial Work Platforms
Working at heights doesn’t have to be a balancing act. Whether you’re navigating a construction site, repairing hard-to-reach areas, or organising a busy warehouse, Aerial Work Platforms (AWPs) are the ultimate game-changer. These innovative machines combine safety and efficiency, making elevated tasks not only easier but also far less risky. In this blog, we’ll explore the key features of AWPs and explain how these versatile machines make working at heights safer, more efficient, and adaptable to various environments. What Are Aerial Work Platforms (AWPs)? Aerial Work Platform (AWP) is a machine designed to lift workers and equipment safely to high places. Also known as aerial work platforms, they are commonly used in industries like: Construction Maintenance Warehousing Utilities Airports Cement Plants Steel Plant Metro Bridges AWPs are used to make tasks at heights, like repairs, installations, or inspections, much easier and safer than traditional methods like ladders or scaffolding. They come in different designs to meet various needs, depending on the job. Types of Aerial Work Platforms Scissor Lifts How they work: A scissor mechanism lifts the platform straight up. Ideal for: Jobs that require a stable, spacious platform at heights, such as electrical work, painting, or warehouse stock picking. Best for: Applications where you need a large working area, such as facility maintenance and construction sites. Lifting capacity: 500–1500 kg Telescopic Boom Lifts How they work: The boom extends straight out to great heights, giving you access to tough-to-reach places. Ideal for: Jobs that need high, straight access with minimal horizontal movement. Best for Outdoor tasks, such as building maintenance, construction work, or any job requiring a direct and high vertical reach. Lifting capacity: 230–450 kg Articulating Boom Lifts How they work: These lifts have joints that allow the platform to move over and around obstacles, providing more flexibility. Ideal for: Jobs that require precise movement and access around obstacles. Best for: Applications like power line maintenance, airports, Metro bridges, industrial applications or jobs requiring flexibility over and around barriers. Lifting capacity: 200–350 kg Key Features of Aerial Work Platforms Designed to simplify challenging tasks at heights, AWPs come equipped with cutting-edge features that prioritize both safety and functionality. Superior Lifting Capacities AWPs come in various lifting capacities to carry more weight, including workers, tools, and heavy equipment. For example, scissor lifts can handle heavier loads, making them great for carrying equipment, while boom lifts provide the necessary reach…
read more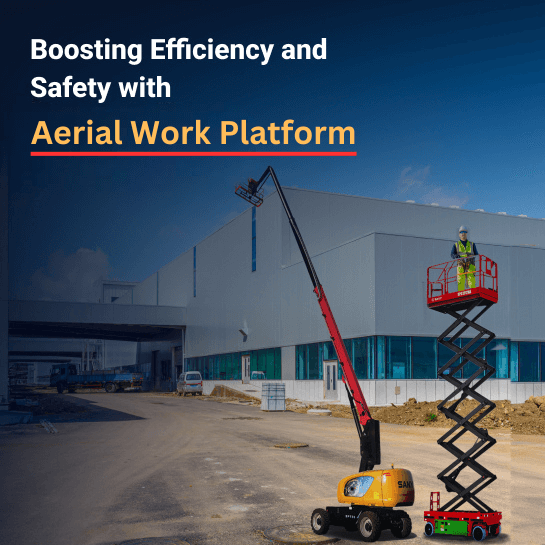
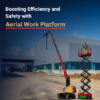
Boosting Efficiency and Safety with aerial work platforms
Elevated workspaces often bring challenges such as inefficiency, safety risks, and high costs when relying on traditional tools like ladders and scaffolding. These limitations can slow down progress and increase operational hazards. AWPs address these issues with solutions that enhance efficiency, improve safety, and reduce operational costs. In this blog, we will explore how Aerial Work Platform are transforming industries and optimising operations. Understanding Aerial Work Platforms An Aerial Work Platform (AWP) is a mechanical device designed to provide temporary access to high or hard-to-reach areas. AWPs come in various forms, each tailored to specific applications: Scissor Lifts: Known for their vertical lifting mechanism, scissor lifts are ideal for tasks that require workers to move straight up and down. They are often used in warehouses, maintenance tasks, and installations where stability is paramount. Articulating Boom Lifts: These lifts have jointed arms that allow vertical as well as horizontal reach, making them perfect for navigating obstacles in confined spaces. Common applications include construction sites and utility maintenance. Telescopic Boom Lifts: Also called straight booms, these boom lifts extend in a straight line, providing maximum reach and height. They are typically used in high-rise construction projects, building maintenance, and heavy equipment servicing. AWP Benefits Aerial Work Platform are redefining how industries operate in elevated workspaces. These innovative tools offer a range of advantages that are game-changing. 1. Efficiency at Its Best Aerial Work Platform are designed to optimise productivity by enabling workers to access elevated areas quickly and safely. Unlike traditional ladders or scaffolding, which require extensive time for setup and repositioning, Aerial Work Platform can be deployed with ease and adjusted swiftly during operations. Their superior manoeuvrability ensures that workers can focus on their tasks rather than wasting time navigating large and heavy equipment. For example, articulating boom lifts allow operators to reach areas around obstacles, while scissor lifts are perfect for vertical tasks in confined spaces like warehouses. By incorporating Aerial Work Platform, businesses can achieve more in less time, leading to faster project completions and cost savings. 2. Enhancing Worker Safety Safety is a cornerstone of any industrial operation, especially when working at heights. Aerial Work Platform provide a secure and stable platform for workers, equipped with features such as: Guardrails to prevent falls. Fall protection systems to secure workers in place. Stable platforms that reduce the risk of instability. Overload protection Angle sensor These features minimise workplace injuries and ensure…
read more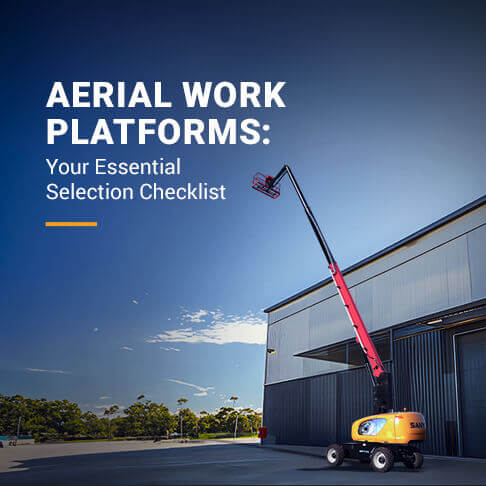
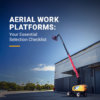
Aerial Work Platforms: Your Essential Selection Checklist
Are you looking for a reliable machine to safely lift workers to perform tasks like repairing overhead electrical wires? For these types of jobs, you require a specialized solution—Aerial Work Platforms. Whether it's for construction, maintenance, or repairs, Aerial Work Platforms (AWPs) are essential tools to ensure safety, increase productivity, and handle tasks at various heights. But with so many options available, how do you know which AWP is the right fit for your project? Let’s dive into this comprehensive guide to help you choose the perfect Aerial Work Platform. What is an Aerial Work Platform? An Aerial Work Platform (AWP) also known as an Elevated Work Platform (EWP) is a mechanical device used to provide temporary access to workers at elevated heights. These platforms are typically equipped with safety features such as guardrails and fall protection systems, allowing workers to safely perform tasks in elevated positions. AWPs are widely used in industries such as construction, maintenance, and warehousing. What are the Major Types of Aerial Work Platforms and Their Applications? When it comes to aerial work platforms, selecting the right one depends on the type of task and the work environment. Below are the major types of aerial lift platforms and their common applications: Telescopic Lifts: Telescopic lifts, also known as straight or stick booms, are perfect for tasks that require extended reach at a fixed height. These are ideal for jobs like tree trimming, construction, and steelwork installations, where a worker needs to access hard-to-reach areas. Boom Lifts: Boom lifts provide more flexibility than telescopic lifts, with extendable arms that can move horizontally and vertically. They are best suited for jobs that require versatile movement, such as electrical maintenance or window cleaning at varying heights and angles. Spider Lifts: Known for their lightweight design and compact structure, spider lifts are perfect for navigating narrow and confined spaces. These lifts are often used in tasks requiring access to difficult areas such as indoor maintenance or confined outdoor spaces. Scissor Lifts: Scissor lifts offer a stable, vertical lifting motion. With a large platform, they are ideal for jobs requiring access to large surface areas at heights, such as painting, roofing, or ceiling installations. Vertical Personnel Lifts: These lifts are lightweight and designed for one person. They are used primarily for indoor jobs like changing light bulbs or performing repairs in warehouses or offices. Articulated Lifts Also known as knuckle booms,…
read more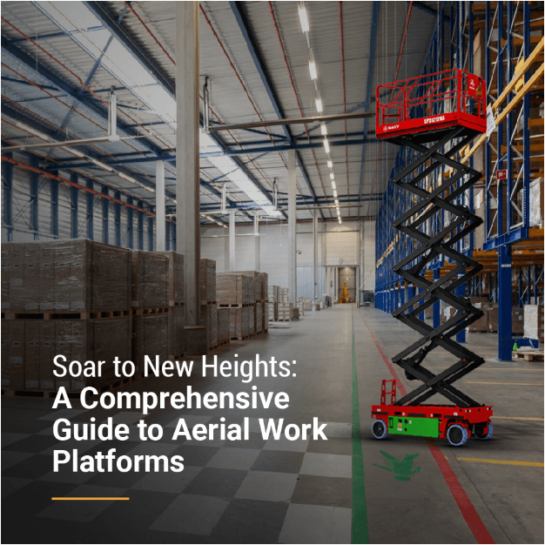
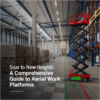
Soar To New Heights: A Comprehensive Guide To Aerial Work Platforms
In the ever-evolving landscape of construction, maintenance, and industrial operations, Aerial Work Platforms (AWPs) play a crucial role in reaching new heights—literally and figuratively. This comprehensive guide delves into the various types of AWPs, their essential safety features, and best practices for maintenance and inspection. Whether you are an industry professional, facility manager, or simply interested in the mechanics of high-access equipment, this guide will provide valuable insights into selecting, operating, and maintaining AWPs to ensure safety, efficiency, and optimal performance. What is an Aerial Work Platform (AWP)? An Aerial Work Platform (AWP) is a mechanical device designed to provide elevated access for personnel and equipment to perform tasks at height. Commonly referred to as aerial lifts, these platforms include various types such as scissor lifts, boom lifts, and personnel lifts. They are equipped with a platform or basket supported by hydraulic, pneumatic, or mechanical systems that allow for vertical and horizontal movement. AWPs are utilized in construction, maintenance, and industrial applications to enhance safety and efficiency when working at elevated positions, adhering to strict safety standards and operational guidelines. Types of Aerial Work Platforms Aerial Work Platforms come in various options, offering easy accessibility for different use cases. Some are optimized for indoor or outdoor use, some for people or equipment, and some for flat or rough surfaces. Here are some of the most common types of Aerial Work Platforms. Scissor Lifts Scissor lifts have a platform that rises vertically using a crisscrossing mechanism of linked, folding supports. They offer stable, high-reaching access for tasks requiring substantial horizontal workspace and are ideal for indoor use or flat surfaces. Boom Lifts Boom lifts feature a platform mounted on an extendable arm or boom, which allows both vertical and horizontal reach. They come in two main types: telescoping (straight) and articulating (knuckle) booms, providing flexibility for accessing hard-to-reach areas. Vertical Mast Lifts These compact lifts have a narrow base and a vertical mast that extends upwards, offering access to high places in tight spaces. They are suitable for indoor applications and are often used for maintenance tasks. Personal Lift Platforms Designed for individual use, these lifts are typically smaller and more portable. They provide access to elevated areas with limited space and are used for tasks like shelving, lighting maintenance, and other small-scale applications. Trailer-Mounted Lifts Also known as tow-behind lifts, these are mounted on a trailer and can be towed…
read more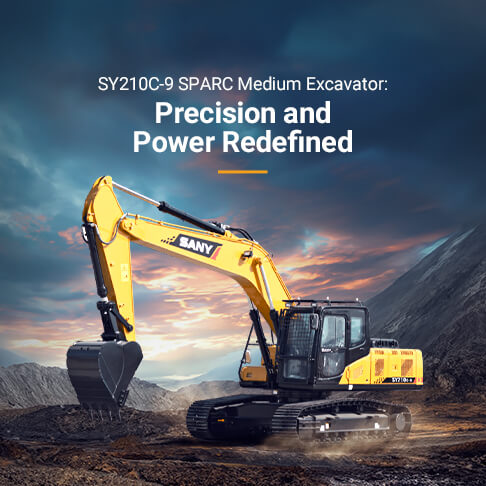
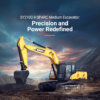
SY210C-9 SPARC Medium Excavator: Precision and Power Redefined
Harness the force of a thunderstorm with the precision of a scalpel—SANY Sparc Medium Excavators deliver raw power that is finely controlled for any challenge. The immense versatility of this machine facilitates its vital role in the construction, mining, and infrastructure sectors. We'll look at SANY’s medium excavator, SY210C-9 SPARC, diving into its unique features that combine advanced technology with robust engineering to ensure it meets the toughest demands. From fuel efficiency and low maintenance costs to intelligent control systems and exceptional durability, let's discover how SANY's medium excavator excels in performance and offers significant cost savings and operational benefits, making it the top choice for professionals in the industry. What are Medium Excavators Used For? Medium excavators are versatile machines that play a critical role in construction, mining, and infrastructure projects. Their mid-sized design lets them handle various tasks that require strength and precision. These machines possess enough power to handle heavy loads, break through tough materials, and perform continuous operations without faltering. Precision is crucial for tasks that require delicate handling, such as trenching near existing structures or grading land with exact specifications. The ability to control such power with finesse ensures that medium excavators can perform a wide range of tasks efficiently. This balance is what sets these medium excavators apart. SY210C-9 SPARC: Robust and Reliable The SY210C-9 SPARC medium excavator, equipped with a Cummins 6BT5.9-C140 engine and weighs 21 tons. It is built for reliability with a strengthened structure and low maintenance cost. This mid-size excavator features DOMCS Intelligent Control and advanced monitoring systems for optimal performance. It ensures exceptional durability through its sturdy undercarriage and robust components, making it well-suited for demanding tasks and challenging environments. This focus on durability is complemented by the machine's design for low maintenance costs, maximizing customer savings through high fuel efficiency and minimal upkeep requirements. The SY210C-9 SPARC leads its class in intelligence and reliability thanks to its advanced monitoring features. Equipped with GPRS monitoring, remote error diagnosis, and smart alerts, which help in providing real-time data and insights. If you are looking for a 20-ton excavator, this might be the perfect choice for you. Fuel Efficiency SANY's medium excavators are equipped with highly efficient engines that significantly reduce fuel consumption, leading to lower operational costs. These engines are designed to optimize power output while minimizing fuel use, ensuring that your projects are both cost-effective and environmentally friendly. This…
read more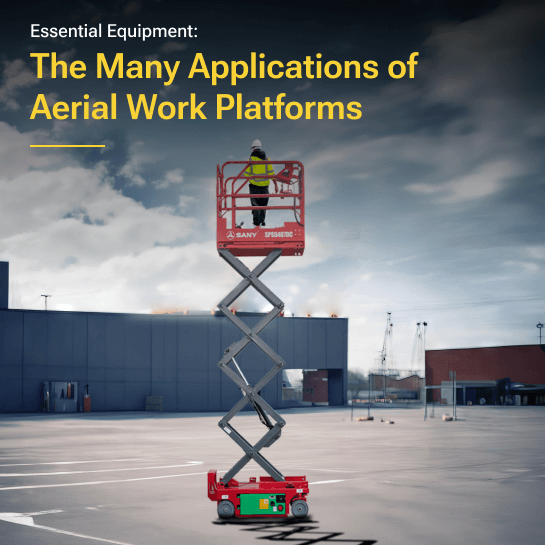
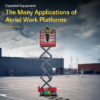
Essential Equipment: The Many Applications of Aerial Work Platforms
Have you considered the challenges of performing maintenance tasks at heights of 18 to 20 meters above ground? For such elevated tasks, a specialized solution is essential—this is where Aerial Work Platforms (AWPs), or aerial lifts, come into play. Whether you’re handling logistics in a warehouse or working on the exterior of a high-rise building, these platforms provide a secure way to access elevated spaces. This post delves into the top applications of aerial work platforms and how they support efficient and safe operations. What Are The Different Types of AWPs? The main types of Aerial Work Platforms (AWPs) include: 1. Scissor Lifts: Designed for vertical lifting, scissor lifts provide a stable platform for workers to reach high areas directly above the base. They are ideal for indoor and outdoor tasks such as maintenance, repairs, and installations. 2. Articulating Boom Lifts: These lifts have jointed arms that allow for flexible positioning, enabling operators to reach around obstacles. They are perfect for applications requiring access to confined or hard-to-reach spaces, such as construction and electrical work. 3. Boom Lifts: Also known as straight or stick booms, these lifts extend directly outward, providing maximum reach and height. They are commonly used for projects that require access to extreme heights or far-reaching tasks, such as high-rise building maintenance and heavy equipment servicing. Top Applications of Aerial Work Platforms Aerial lift applications span a wide range of industries providing safe and efficient access to high and hard-to-reach areas. Here are the uses of AWPs: 1. Construction Sites Construction sites are one of the most common places to find aerial work platforms. AWPs enable workers to safely reach heights necessary for tasks such as installing structural elements, painting, and inspecting high areas. The mobility and flexibility offered by platforms like scissor lifts and telescopic boom lifts make them ideal for construction environments. They allow workers to carry out complex tasks safely and efficiently, with minimal setup time. 2. Manufacturing Factories In manufacturing settings, aerial work platforms play a vital role in facilitating equipment maintenance, assembly line adjustments, and other high-elevation tasks. Articulating boom lifts, for example, can navigate around machinery and other obstacles, offering precise placement for tasks requiring elevated access. This efficiency enables factories to maintain high productivity without compromising worker safety. 3. Producing and Servicing Heavy Equipment AWPs are crucial in industries that produce and service heavy equipment. These machines often require precise…
read more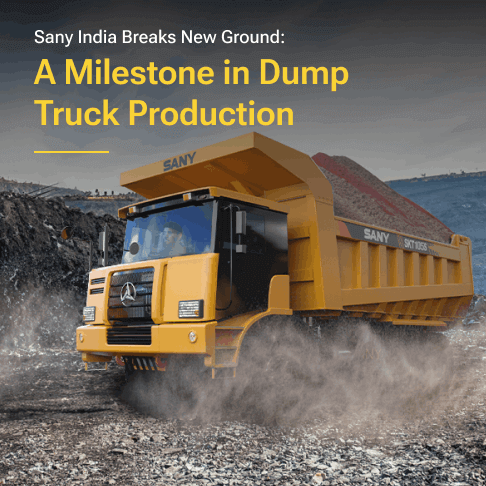
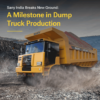
SANY India Breaks New Ground: A Milestone in Dump Truck Production
At SANY India, we’re excited to share a new chapter in our journey—a milestone that reflects our commitment to innovation, quality, and sustainability. With over 1,000 mining dump trucks in our Pune factory, we’re proud to support India’s ‘Make in India’ initiative and drive forward advancements in mining and construction. By setting new standards for durability, fuel efficiency, and operator comfort, we are transforming the mining equipment landscape and contributing to India’s industrial growth. Building India’s Industrial Backbone: SANY’s Journey of Excellence Established in 1989, SANY India has been at the forefront of the global construction and mining equipment industry. Here in India, we’ve built a reputation for delivering top-notch machinery that empowers industries and contributes to the nation’s growth. Our Pune facility is the backbone of this mission, bringing world-class manufacturing and innovation to support India’s rapid industrialisation. A Production Milestone That Speaks Volumes Our recent achievement is truly remarkable. Here’s a closer look at the specifics: Milestone: SANY India’s Pune plant has manufactured over 1,000 mining dump trucks, meeting rising demand in a short span of time. Models Contributing: The milestone includes the production of the SKT90S, SKT105S, and SLT05E models, each designed to meet the needs of India’s mining and construction industries. Timeline: This accomplishment was reached by October, showcasing SANY’s efficient manufacturing capabilities. Production Facility: The Chakan plant in Pune is equipped with advanced machinery and quality control processes. This state-of-the-art facility is instrumental in ensuring every SANY dump truck meets stringent quality standards, aligning with the ‘Make in India’ vision. Driving the Future with Fuel Efficiency and Advanced Engineering SANY India’s mining dump trucks are renowned for technology and innovation. Here’s how each model stands out: Fuel Efficiency: The SKT90S and SKT105S models are designed with fuel efficiency in mind, ensuring lower operational costs even in the harshest conditions. Electric Innovation - SLT05E: The SLT05E model takes efficiency a step further with a regenerative battery that charges itself when descending and consumes minimal energy when ascending. This technology enhances both fuel efficiency and sustainability. Operator Comfort: We understand the importance of comfort for operators working long hours. The trucks feature air-conditioned cabins and ergonomic controls, creating a comfortable and safe workspace. Durability & Continuous Operation: These mining dump trucks are built to work day and night with minimal downtime, ensuring that projects stay on track and productivity remains high. R&D and Quality Standards SANY’s research…
read more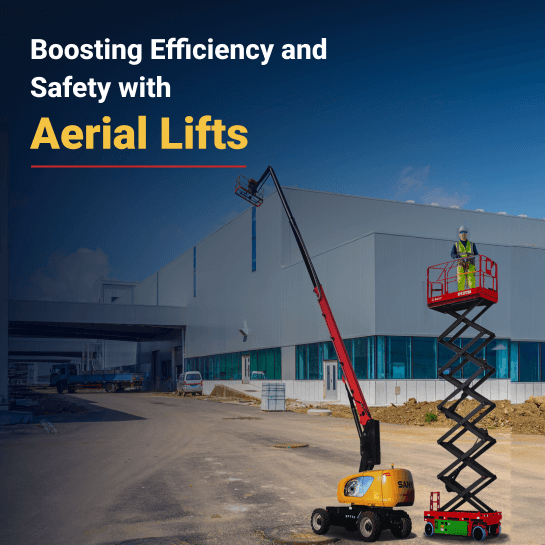
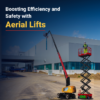
Unleashing the Potential of Excavators: Applications in Construction
Excavator machines are revolutionising the construction industry by unlocking new levels of efficiency, versatility, and innovation. With the ability to handle a wide range of tasks, from digging and lifting to demolition and material handling, excavators are essential for modern construction projects. As the demand for faster project timelines, precision, and sustainability grows, excavators are becoming indispensable tools for maximising productivity and reducing operational costs. With innovations in design and technology, excavators are now pushing the boundaries of what’s possible, enabling construction companies to tackle complex tasks with ease. Uses of Excavators in Construction Excavators are a vital part of construction projects, offering unmatched versatility and efficiency. From small-scale tasks to large infrastructure developments, excavators in construction ensure that jobs are completed with precision and speed. 1. Digging Foundations and Trenches One of the primary excavator uses is digging foundations and trenches for buildings and infrastructure projects. Excavators in construction ensure precision in excavation, allowing for accurate depth and alignment. These machines make foundation work more efficient, reducing the time and labor required for manual digging. 2. Material Handling With the right attachments, excavators excel at handling heavy materials. Construction sites often require the movement of large objects such as pipes, steel beams, and concrete blocks. Excavators simplify these tasks by lifting and transporting materials with ease, ensuring safety and speed. This capability reduces the need for additional equipment and minimizes workplace hazards, streamlining the entire construction process. 3. Demolition Excavator machines equipped with specialized attachments like hydraulic breakers, claws, and cutters are ideal for demolition projects. Whether tearing down buildings or removing old infrastructure, excavators bring precision and power to these tasks. Their ability to perform controlled demolition reduces the risk of damage to surrounding structures. Additionally, their versatility allows them to handle debris removal, making them a one-stop solution for demolition tasks. 4. Landscaping and Earthmoving For projects that involve shaping terrain or preparing land, excavators play a crucial role. They are used for grading, leveling, and clearing sites, ensuring the land is ready for construction. Excavator machines help create smooth and stable surfaces, which are essential for building foundations and roadways. Their ability to work on uneven terrain makes them indispensable for landscaping projects. 5. Dredging and Waterway Maintenance In projects involving water bodies, excavator uses extend to dredging rivers, canals, and ponds. Long-reach excavators are particularly suited for this purpose, as they can remove silt, debris,…
read more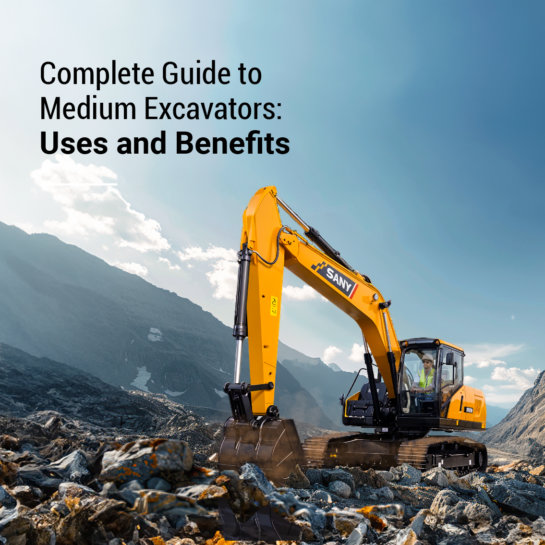
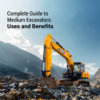
Complete Guide to Medium Excavators: Uses and Benefits
When it comes to tackling the diverse challenges of construction, one piece of equipment stands out for its versatility and power: the medium-sized excavator. Whether you're starting a project, reshaping the land, or lifting heavy materials, medium excavators are the backbone of construction. In this blog, we will discuss the mid-size excavator's types and sizes, applications and benefits. Apart from this, you will get tips for selecting the right mid-size excavator for your business. Mid-size Excavators Mid-size excavators, often referred to as medium excavators are typically crawler excavators with weights ranging between 15 to 34 tons. These excavators are versatile machines that balance the power of larger excavators with the maneuverability of smaller ones. Mid-size excavators provide an ideal balance of power and maneuverability, making them versatile tools for a wide range of tasks such as digging, trenching, and demolition. Their compact size allows them to operate effectively in confined spaces, while still delivering the strength required for demanding jobs. Additionally, they are cost-effective, with lower fuel consumption and maintenance needs, and are easier to transport compared to larger machines. With advanced cab features and the ability to use various attachments, mid-size excavators enhance productivity and adaptability, making them a valuable asset for diverse construction, landscaping, and utility projects. Where Do We Use Mid-size Excavators? Mid-size excavators are a popular choice in many industries due to their versatility, power, and ability to operate in both large and confined spaces. Here are some tasks for which the mid-size excavator is the ideal option: Construction Sites: Mid-size excavators are widely used in general construction projects. Their size allows them to perform tasks such as digging foundations, trenching, and grading with efficiency. Landscaping: They are also popular in landscaping projects where they are used for tasks like moving soil, creating ponds, or removing trees and large stumps. Road Construction: In road construction, mid-size excavators are used for digging trenches for utilities, removing pavement, or grading road surfaces. Utility Work: These machines are ideal for utility installation projects, such as laying pipes or cables, because they offer enough power to dig deep trenches while remaining compact enough to operate in tighter spaces. Demolition: Mid-size excavators are often employed in demolition projects where they can tear down small to medium-sized structures, break up concrete, and remove debris. Mining and Quarrying: In smaller mining and quarrying operations, mid-size excavators are used for tasks such as digging…
read more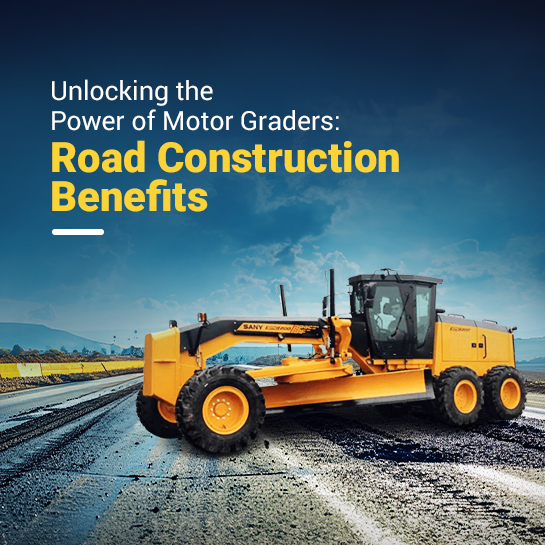
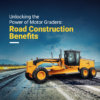
Unlocking the Power of Motor Graders: Road Construction Benefits
In the world of road construction, the motor grader stands out as a key player, an indispensable tool that ensures the smoothness, precision, and durability of our roadways. Whether you're a seasoned contractor or a newcomer to the construction industry, understanding the importance and capabilities of motor graders is crucial. This blog will delve into the essential features of motor grader machines, their role in road construction projects, and the numerous benefits they offer, from precision grading to enhanced efficiency. What is a Motor Grader? It is a heavy construction machine equipped with a long blade used to create a flat surface during the grading process. Motor grader equipment is typically utilized in the construction and maintenance of roads, offering the precision needed to achieve a smooth and even surface, which is vital for road quality and longevity. Essential Features of Motor Grader Equipment Motor graders are designed with several features that make them indispensable in road construction: Precision Grading: The primary function of a motor grader machine is to create a level surface. The blade of a motor grader can be adjusted to various angles, pitches, and heights, allowing operators to grade with exceptional accuracy. This precision is essential for laying a stable foundation for roads, ensuring that the surface is even and properly contoured to support subsequent layers of asphalt or concrete. Durability: Motor grader equipment is built to withstand the rigors of tough construction environments. With robust engines and high-quality materials, these machines are designed for long-term use. Their durability not only reduces the frequency of maintenance but also ensures consistent performance across multiple projects. Versatility: Motor graders are incredibly versatile. They can be used for a variety of tasks beyond road construction, such as leveling soil, and spreading materials. This versatility makes them a valuable investment for construction companies, as they can be used year-round for different applications. Advanced Technology: Modern motor grader machines come equipped with advanced technology, such as GPS and laser systems, which further enhance their precision and efficiency. These technologies allow operators to execute complex grading tasks with ease, reducing the likelihood of errors and the need for rework. Benefits of Using Motor Graders in Road Construction The benefits of using motor graders in road construction projects are manifold. Here’s how these machines contribute to the success of such projects: Enhanced Efficiency: Motor graders streamline the grading process, making it faster and…
read more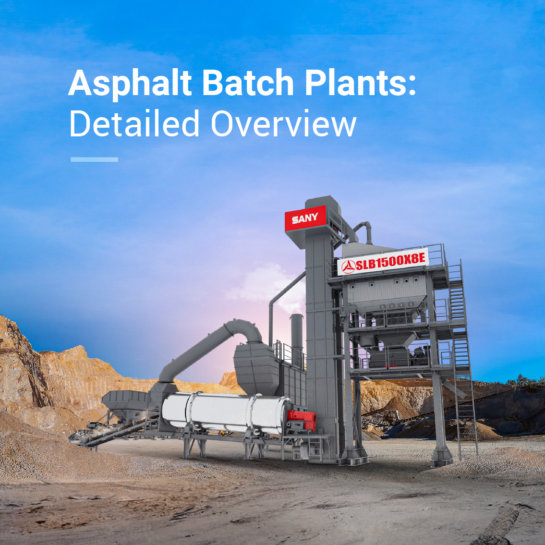
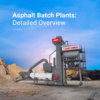
A Complete Guide to Understanding Asphalt Batch Plants
Understanding the asphalt batch plant ensures the production of high-quality asphalt, which is essential for creating durable and long-lasting roads. Not only that, it also enhances efficiency by optimizing the use of materials for road construction. This knowledge is key to maintaining strict quality control, reducing the risk of defects, and assuring the asphalt meets specific project requirements. In this blog, we will explore asphalt batch plants, their working principles, and their essential role in successful construction projects, contributing to improved roads and infrastructure. What is an Asphalt Batch Plant? An asphalt batch plant is a facility that produces hot mix asphalt in batches rather than in a continuous process. These plants are highly flexible and capable of producing different types of asphalt mixtures, such as hot mix asphalt (HMA), warm mix asphalt (WMA), and cold mix asphalt (CMA). The versatility and precision in the mixing process make asphalt batch plants ideal for various road construction projects, ranging from small repairs to large highway developments. Key components of Asphalt Batch Plant Here are the various key components of the Asphalt Batch Plant: Cold Feeder Bins: These bins store different sizes of aggregates and feed them into the system in controlled amounts. They ensure a steady and precise supply of raw materials to the drying drum. Conveyor: A conveyor belt transports the cold aggregates from the feeder bins to the dryer drum. It facilitates continuous movement and consistent feed of aggregates into the system. Drying Drum: The drying drum heats the aggregates to remove moisture and achieve the desired temperature. It is equipped with a powerful burner to ensure efficient heating. Elevator: This component lifts the heated aggregates from the drying drum to the vibrating screen. It ensures the smooth transfer of materials for further processing. Vibrating Screen: The vibrating screen separates the hot mix into various compartments based on size. It ensures precise classification of aggregates before mixing. Hot Bins: Hot bins temporarily store the heated and classified aggregates before they are weighed. They ensure the availability of the right amount of materials for mixing. Weighing Systems: These systems measure precise amounts of filler, aggregate, and bitumen. They are crucial for maintaining the correct proportions in the asphalt mix. Pugmill Mixing Unit: The pugmill mixing unit thoroughly mixes the weighed ingredients to create the hot mix asphalt. It ensures a homogeneous and high-quality mix. Dust Collection System: This system collects…
read more